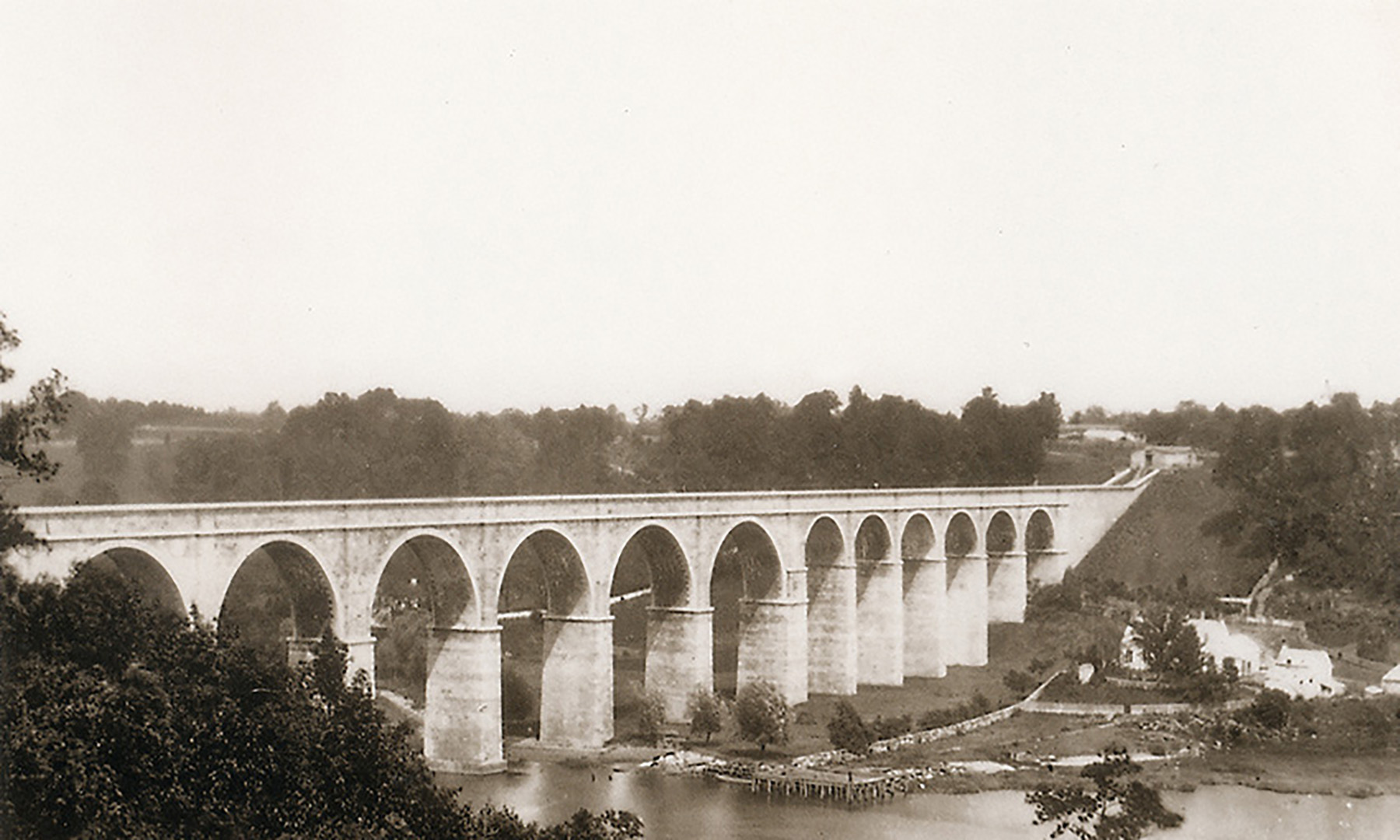
By Leslie Nemo
New York City might have a reputation as a place where people can find anything they might want at any time of day. But for the first 217 years of its existence, the city only occasionally offered a glass of clean water.
That changed when the Old Croton Aqueduct began operating in 1842. Running from the Croton River upstate into two city reservoirs, the approximately 40 mi system was the first to bring high volumes of clean water into New York City. Writers describing the system as it was being built drew comparisons between the aqueduct and its Roman counterparts, even if it did not have quite the staying power as some of the ancient versions: Sections now sit underwater, and the city replaced it after 51 years of service, according to George H. Rappole in his article “The Old Croton Aqueduct.”
The first flush of drinkable water offered by the original Croton Aqueduct quenched the thirst of residents very well. And as the population continued to grow, so did the demand for high-quality water.
When the Dutch arrived on Manhattan in the 1620s, water sources available on the island met their needs for a few decades. The 48-acre Collect Pond in lower Manhattan was popular for a while, and in 1667 the first public well was dug near what is now Battery Park, according to the NYC Environmental Protection Department in the article, “History of New York City Drinking Water.” The well made use of a pump that brought the water to the surface — another first. As the mid-to-late 1700s approached, population numbers were surpassing what these ponds and wells could offer.
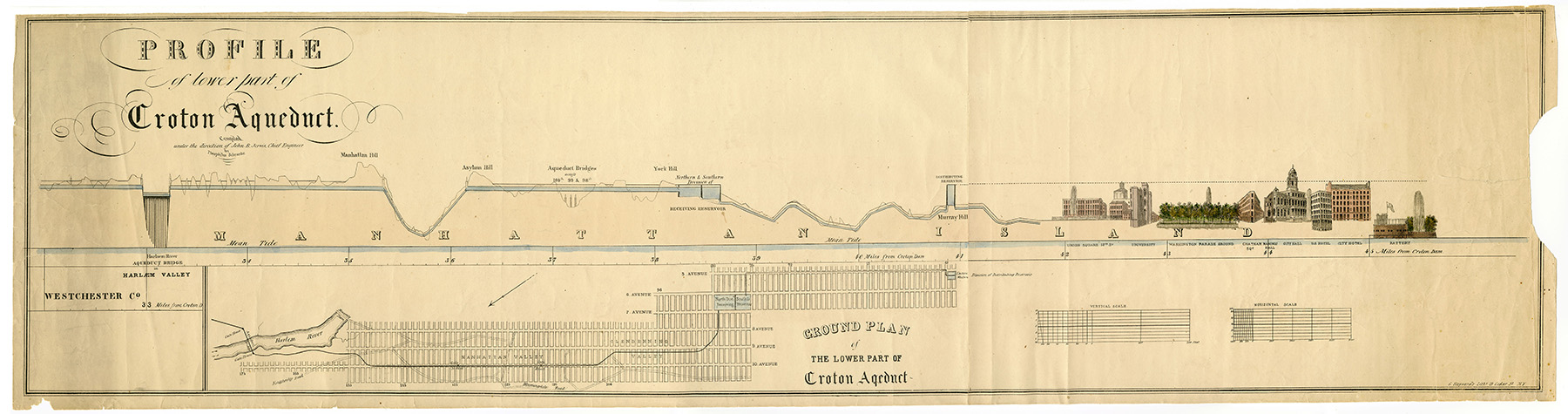
By 1748, for example, a well known as the Old Tea-Water Pump drew lines of residents who would patiently wait to draw from the only option in the area offering something drinkable, according to Edward Wegmann in his book The Water-Supply of the City of New York. 1658-1895.
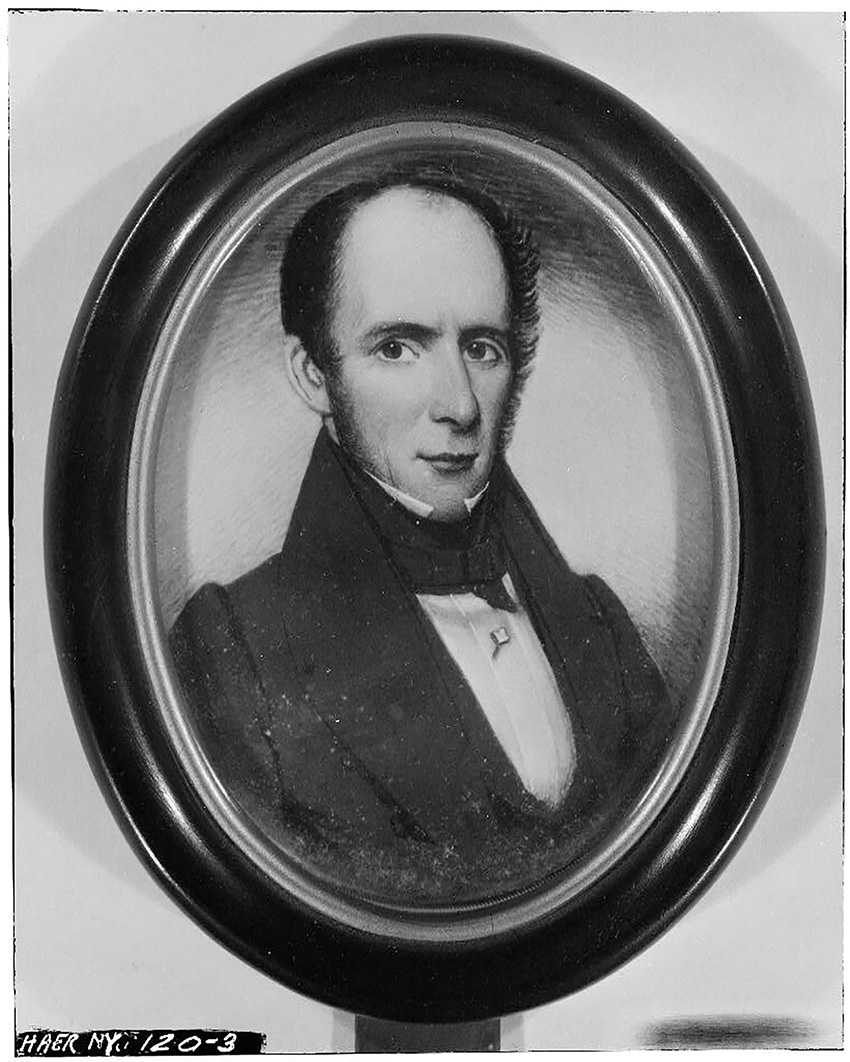
The parched status of the city also appeared in sickness and flames. By the end of the 18th century, the water supply from Collect Pond had become polluted, primarily due to waste dumped by industries that had been built along its shores and the presence of organic matter. After a yellow fever outbreak swept through the city in 1798, a local physician wrote that the “large stagnating, filthy” pond was causing illness and was insufficient for the number of residents, per Wegmann. In 1828, fires damaged $600,000 worth of property. Firefighters resorted to salt water to put out the blazes, because freshwater was scarce.
The Lyceum of Natural History, the precursor to the New York Academy of Sciences, produced a water report three years later pointing out that human waste was often buried near where water was obtained and that well samples coming from nearby graveyards had a “ropy” appearance, as described by chemist George Chilton in historian Larry D. Lankton’s Historic American Engineering Record NY-120 report “Old Croton Aqueduct.”
The decades of complaints frequently came with requests that the city acquire its water from beyond its borders. The suggestions found a lasting purchase in February 1833, when a state bill was passed, allowing the creation of a Board of Water Commissioners that was authorized to survey land, create designs, and estimate construction costs for an aqueduct — particularly one drawing from the Croton River.
In turn, that same year the commission asked for help from Maj. David Bates Douglass, a former U.S. Military Academy instructor who had worked on a handful of other civil engineering projects. As a consultant for the project, Douglass conducted two examinations — the first in 1833 — of the region. In 1835 after his second examination, he put forth a plan for an aqueduct, estimating the price for the 41 mi long system at $4.8 million.
However, the commission had its own plan for a Croton aqueduct, which it submitted to the Common Council for voter approval. Their estimated cost was slightly lower at $4.25 million.
In April 1835, New Yorkers voted to approve the commission’s water supply system that would start at the Croton Dam at the mouth of the Croton River, traveling through the state, down the island of Manhattan, and into a reservoir in Murray Hill.
Douglass was hired as chief engineer on June 2, setting to work immediately to determine the boundaries of one of the reservoirs that would be behind Croton Dam, working off the plans the commission sketched in February. The aqueduct plans were popular, but their designer was not: The commission fired Douglass for incompetence about a year later and replaced him with John Bloomfield Jervis. Jumping off Douglass’ plans, the new chief engineer finished designs and began putting work out for bid, with construction on the Croton Aqueduct starting on May 16, 1837.
The designs for long stretches of the aqueduct, which Jervis and his team contracted out in sections between 0.4 mi and 0.5 mi long, came with clear instructions. The water-carrying pipe itself was derived from a horseshoe design Douglass had proposed. The bottom, an inverted arch made of brick, morphed into flat sides that sloped outward. Another arch on top made for a protective cover, while concrete lent support to the bottom and sides.
Keeping the 8.5 ft tall and 7.5 ft wide pipe at grade demanded one of two ways of navigating hills. In the areas where the aqueduct’s grade line was below ground, Jervis opted to bury the conduit in the hill, according to Lankton. In areas where the grade line protruded from a hill, Jervis “placed the conduit on a heavy stone foundation wall that reached far enough into the ground to achieve a firm footing,” writes Lankton.
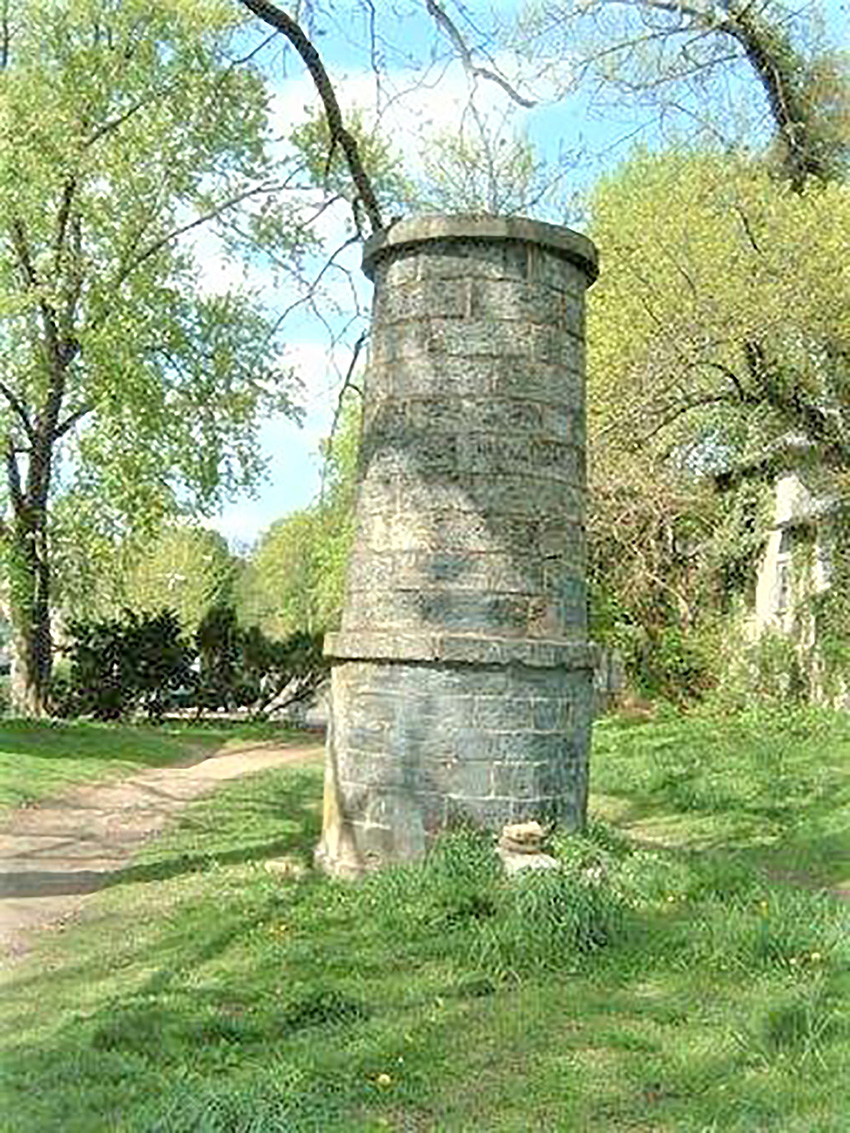
For added protection, on the downhill side Jervis added an embankment. He also added a protective wall made of stone that rested on top of earthen fill and leaned into the conduit, per Lankton. According to the late Robert A. Olmsted, P.E., F.ASCE, in his article “John B. Jervis and the Development of New York City’s Water Supply System,” Jervis also incorporated multiple14 ft tall stone ventilators that stopped air pressure buildup.
These ventilators were placed about every mile down the length of the aqueduct, with every third ventilator being large enough to allow in repair crews. Periodically, Jervis replaced the ventilators with waste weirs.
Work progressed with relatively small hiccups. The concrete base of the aqueduct often cracked when workers tried to lay the material across marshy areas, while nearby residents had to contend with flyrock during construction. Jervis, whose contracts on each segment were known for having exacting demands, strictly guided progress.
One construction crew worked on a Sunday, a day when its designated inspection team was not working. Jervis and the resident engineer overseeing that particular stretch of the aqueduct made the men tear down their work, since the two refused to pay for any work that supervisors were not present to see happen.
Jervis also had a clear idea about alcohol consumption among laborers. The agreements spelled out the expectation that contractors discourage liquor consumption anywhere near the workplace, and project commissioners tried to ban whiskey shops from operating within a mile of a given construction site. Westchester County residents, however, opened taverns on their properties to serve the 4,000 or so workers.
Author Washington Irving, who lived near Tarrytown, New York, wrote to his friends that in their walks back from taverns in the night, laborers claimed they saw headless apparitions around Sleepy Hollow, according to Rappole.
Even if that had been true, the workers had bigger worries. In several instances, contractors offered wages below expectations or reduced pay. On one occasion in 1840, the contractors reduced daily pay from $1 to 75 cents. When the workers went on strike due to the pay cut, officials called in a militia to push back.
By the time labor protests were igniting, Jervis was fighting his own work battles. Most of the aqueduct ran along land, save the portion that would have to cross the Harlem River Valley — what would become the High Bridge. At the water commission’s request, Jervis submitted two designs to close the gap: one that carried the aqueduct on a series of piers high above the water and one — a syphon — that descended and rose with the valley, bringing water through multiple 36 in. diameter pipes and sitting 4 ft above the water at its lowest. The second option (at about $426,000) cost less than half the first and became Jervis and the commission’s preferred design.
However, a January 1838 report from the commission endorsing the lower bridge went over poorly with the public. As laid out in a letter in March 1938 in the American, a local newspaper, the sentiment was that the low bridge’s boat clearance was inadequate and would keep the largely unnavigable Harlem River from being developed into a navigable one. A year later in the spring of 1839, the state legislature passed a bill stipulating the aqueduct crossing the river would either have to go under the water or clear it by at least 100 ft at high water mark.
Jervis returned to his original high bridge design, albeit a version that was 12 ft lower than in his first plan. And to meet the legislature’s demands, he lowered the undersides of the bridge arches to 100 ft above high water, per Lankton. He also added a shallow, inverted syphon to keep the water flowing, since the reduced height brought the conduit below the grade line.
Unsurprisingly, the bridge over the Harlem proved to be a challenge to build as well as costly. It was, as one contemporary chronicler put it, “the next disappointment” in the aqueduct’s construction, as related in Charles King’s A Memoir of the Construction, Cost, and Capacity of the Croton Aqueduct, Compiled from Official Documents.
Previously, one of Jervis’ crews had sounded out the river and located what the team thought was competent bedrock that the piers could rest on below the water. Excavations, however, showed this was wrong. Instead, the riverbed was full of boulders that were not an adequate foundation for the cofferdams. The contractor had to drill into the boulders and heave them out of the way. In the end, five land and one river pier settled on bedrock while 10 others rested on oak piles that extended 30 ft to 45 ft into overburden sand.
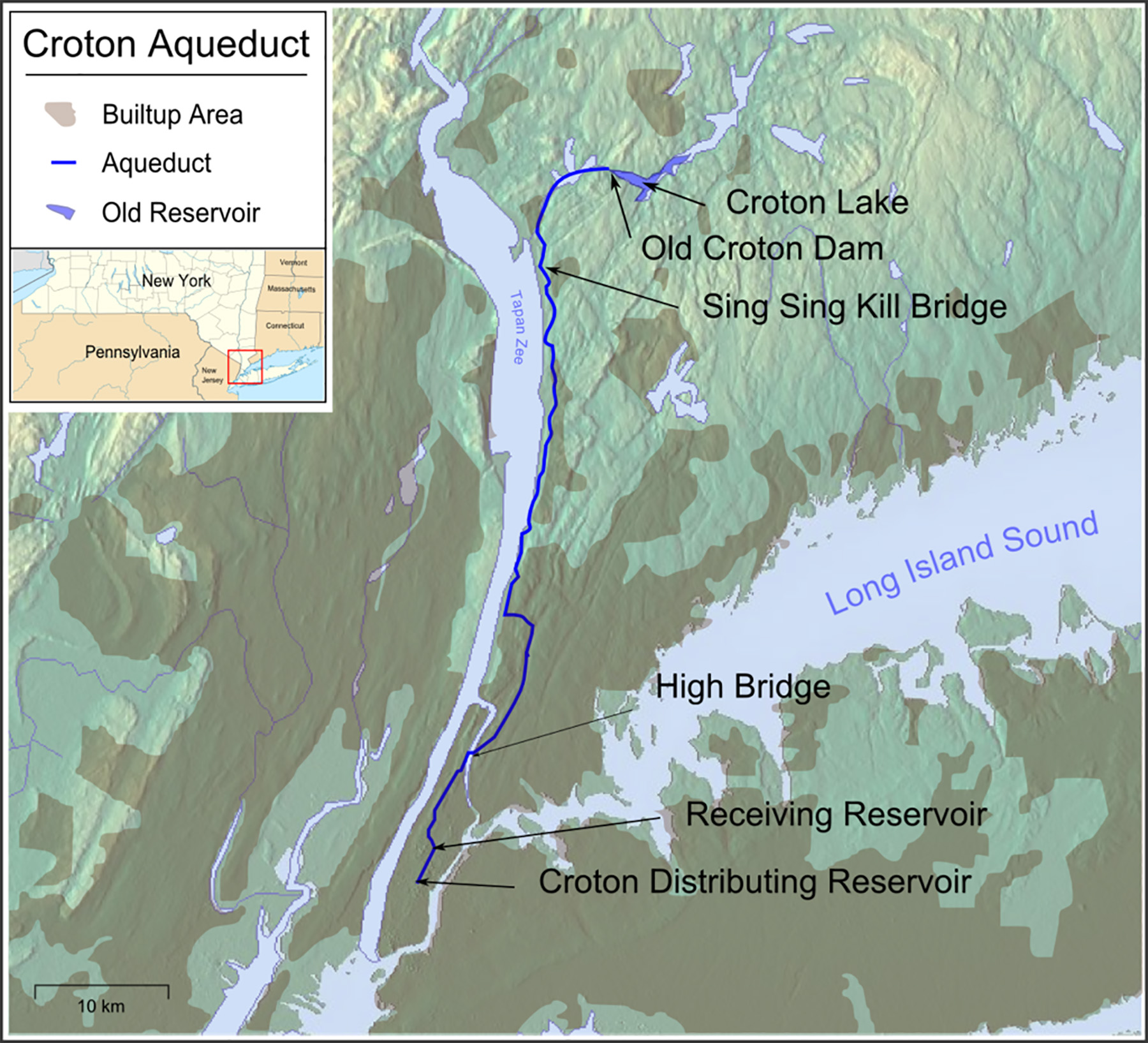
The Harlem River headaches eventually seemed like minor annoyances in comparison with the issues Jervis encountered at the aqueduct’s origin. Bringing water into the city required a masonry dam in the Croton River, the location of which Douglass had somewhat approximated.
When Jervis’ team members looked for a more precise location, bedrock across the channel was scarcer than Jervis was hoping it would be. In order to remain on bedrock — and not extend the masonry dam onto gravel — Jervis redesigned the dam, shortening it from 100 ft wide to 90 ft wide, which left a gap. To complete the rest of the dam, he added an earthen embankment.
The chief engineer also designed a hollowed-out bluff on the southern end. A 180 ft tunnel cut through the rock, Jervis determined, would lead water through an “arch in the bulkhead” of the gatehouse, a screen, and a series of gates before emptying into the aqueduct, according to Rappole.
Construction was partially completed in January 1841 when a rainstorm came down on a thick blanket of snow and flooded the Croton. The water was too much for the unfinished dam to handle. Rising over the top of the weir, the water washed away the embankment and flooded the nearby community, destroying homes and businesses and killing three people. “No one without such experience could imagine the severity with which this scene, with its attending circumstances, affected me,” wrote Jervis in a compilation of letters edited by Neal FitzSimons.
Despite this tragedy, there was some good news: The original masonry weir remained intact. According to Lankton, Jervis realized “he had no choice except to build on gravel, in order to make the overflow weir longer.”
To do that, he added an extension — 180 ft — that was founded on piers comprising alternating layers of white oak and stone, according to Rappole. These piers sandwiched a hydraulic masonry core on either side. Jervis also gave the weir an ogive (or reversed) curve, and 300 ft downstream he installed a secondary dam to make a stilling basin, with both choices meant to lessen the odds that the constructed foundation would erode.
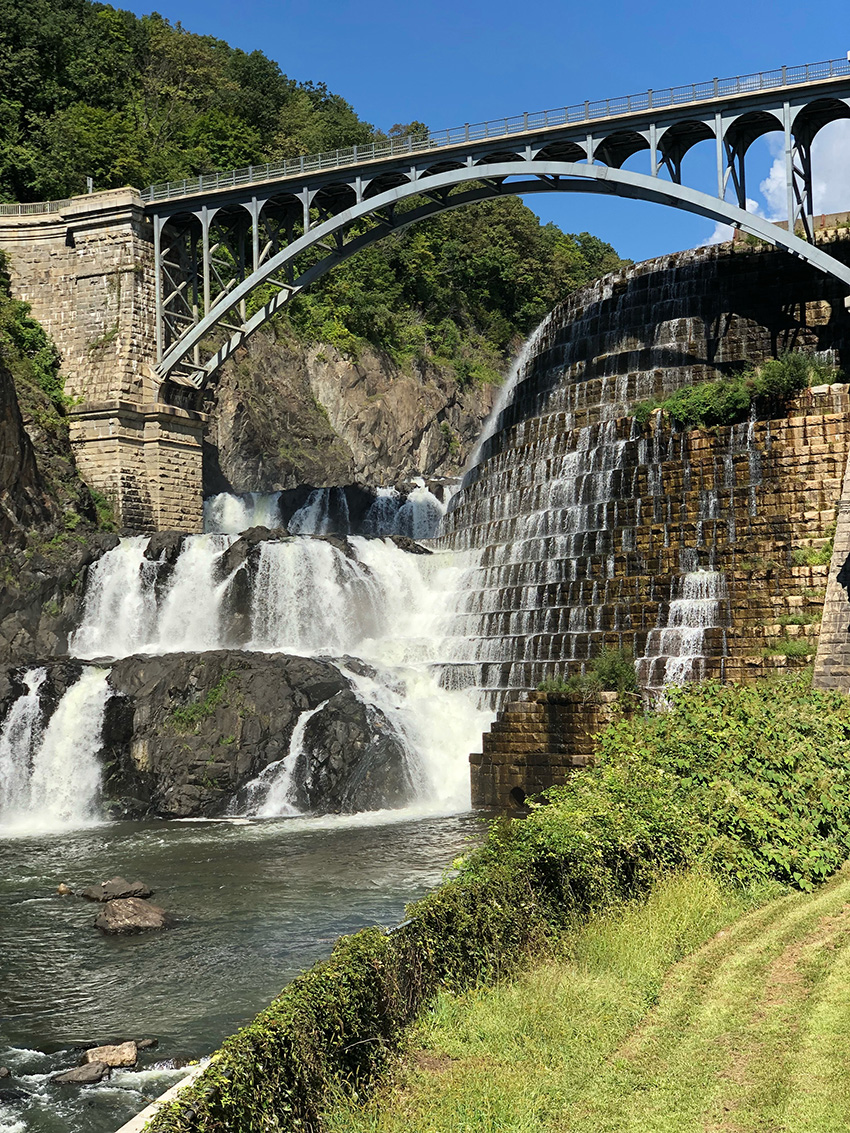
The secondary dam also reduced the force of the water falling over the weir, which in turn lessened the potential for the riverbed to erode.
About a year and a half after the disastrous Croton flood, the entire aqueduct was nearly finished. The structures and equipment needed to deliver clean Croton water around the city were ready too. The receiving reservoir — which sat in what was then York Hill and is now Central Park — was a 1,826 ft by 836 ft rectangle blasted into primarily solid rock. Iron pipes ran from the receiving reservoir to the distributing reservoir on Murray Hill.
Measuring 420 ft by 386 ft, the reservoir could hold 21 million gal. that would be distributed to residents via another 134 mi of pipes. Railings and an 18 ft wide green path around its perimeter allowed people to stroll what was essentially a small lake. As for the final appearance, writes Lankton, “no stylistic catchwords used to describe American architecture of the period fit it.”
On June 8,1842, Jervis and his colleagues conducted one of their final inspections of the aqueduct by walking about 30 mi from the Croton Dam to the Harlem River. On June 22, the team performed its last inspection before opening, but this time by boat.
The headgates had been opened, so the team took the Croton Maid, a four-person boat down the Manhattan portion of the construction at a breakneck 2 mph.
On June 27, water flowed into the receiving reservoir, and on July 4, residents walked the Murray Hill promenade and watched as the long-awaited water filled the distributing reservoir.
Construction of the Croton Water Supply System, including land bought in Westchester County, cost $8,575,000 — $12,500,000 if city distribution pipes and interest on the necessary loans are included — and gave the city more water than it was prepared for. In 1854, the city debuted a police force dedicated to monitoring the reservoirs and fining people who used the Croton supply for washing streets.
Growing water consumption pushed the city to build the larger New Croton Aqueduct in 1893. Jervis’ designs and the labor of thousands of people became obsolete — for all the frustration the Croton Dam gave Jervis, his structure was submerged by the New Croton Dam.
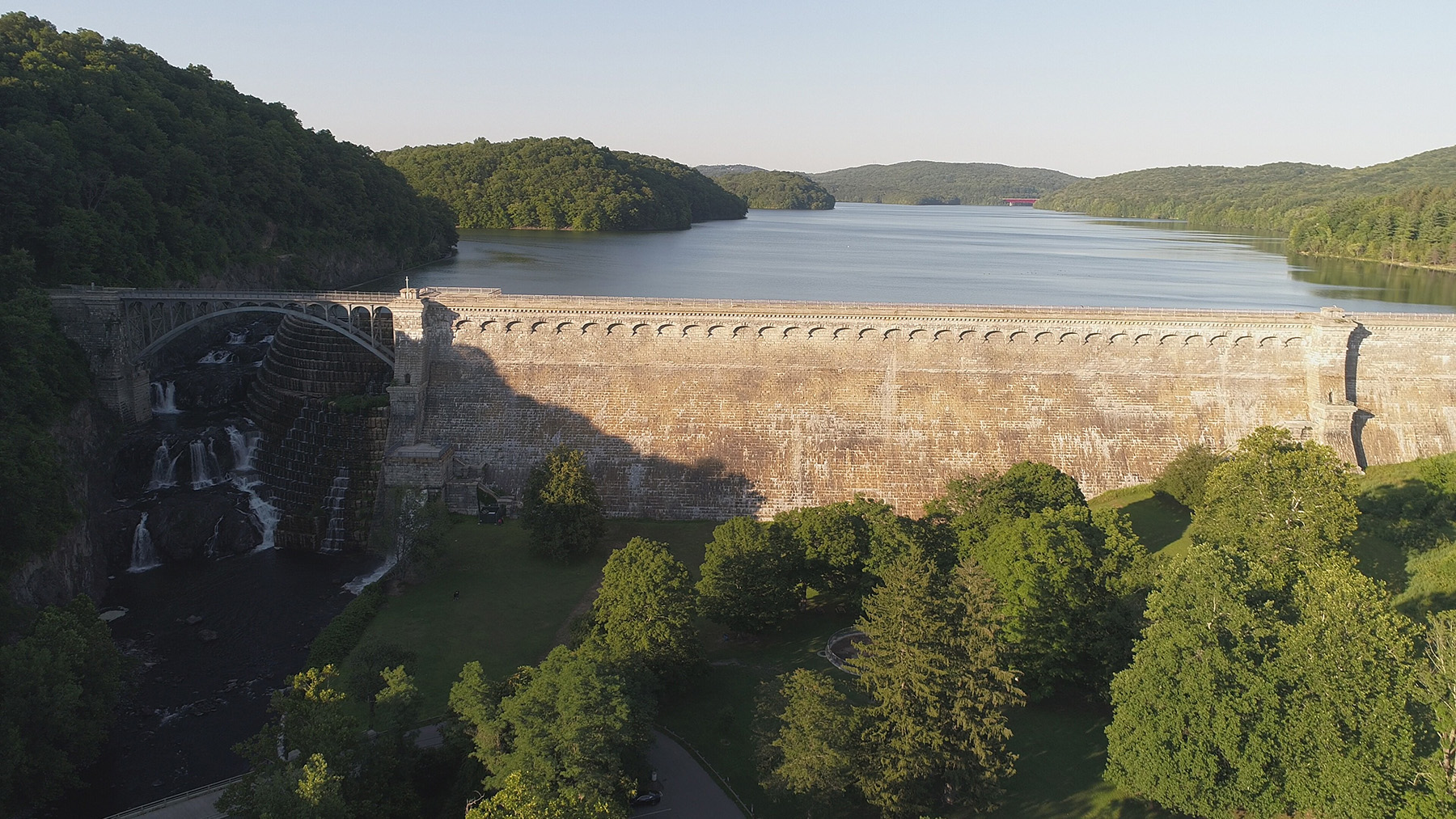
In 1971, New York Telephone Co. employees entered a section of the aqueduct to lay cables, revealing that the structure was still sound, according to Rappole, who was allowed to observe the crew as it worked. Quietly holding up for as long as it had might be a fitting legacy for a water system that, even at the time of its construction, had its design and technical achievements overlooked for the service it provided.
On Oct. 16, 1975, the Croton Water Supply System was named a Historic Civil Engineering Landmark.
Leslie Nemo is a journalist based in Brooklyn, New York, who writes about science, culture, and the environment.
References
ASCE Metropolitan Section. Croton Water Supply System.
Collect Pond. (30 August 2022). In Wikipedia.
Crain, E. (17 December 2018,). The Famous Tea Water Pumps of 1700s New York. Ephemeral New York.
FitzSimons, Neal (Ed.). (1971). The Reminiscences of John B. Jervis: Engineer of the Old Croton (page 133) (1st ed.). Syracuse University Press. In Larry D. Lankton, Old Croton Aqueduct. Historic American Engineering Record NY-120.
King, Charles. (1843). A Memoir of the Construction, Cost, and Capacity of the Croton Aqueduct, Compiled from Official Documents. Charles King (printer).
Lankton, Larry D. (1976). Old Croton Aqueduct. Historic American Engineering Record NY-120.
NYC Environmental Protection. History of New York City Drinking Water.
NYCdata and Weissman Center for International Business, Baruch College. (2021). Infrastructure, New City (NYC), the Croton Aqueduct (1840).
Olmsted, Robert A. (2012). John B. Jervis and the Development of New York City’s Water Supply System. In Bernard G. Dennis Jr., Robert J. Kapsch, Robert J. LoConte, Bruce W. Mattheiss, and Steven M. Pennington (Eds.), American Civil Engineering History: The Pioneering Years (pages 371-378). Fourth National Congress on Civil Engineering History and Heritage.
Rappole, George H. (1978). The Old Croton Aqueduct. IA: The Journal of the Society for Industrial Archeology, Vol. 4, No. 1, pages 15-25.
Roberts, Sam (14 July 2008). New York’s Birth Date: Don’t Go by City’s Seal. The New York Times.
Wegmann, Edward (1896). The Water-Supply of the City of New York. 1658-1895 (1st ed.). John Wiley & Sons.
This article first appeared in the March/April 2023 issue of Civil Engineering as “Bringing Clean Water to the Big City.”